
Omnid mobile collaborative robots (Omnid mocobots) collaborate with each other and one or more human operators. Developed over five years, the project explores human-robot interaction in physically demanding environments where teams of robots could help workers manipulate a variety of large, articulated, or flexible objects without the physical hardship.
In the video, three omnid cobots help me attach a model plane wing to a test aircraft body. While this would be extremely challenging for one person and difficult even for a group of people, it becomes simple when a single worker coordinates with robots that can counteract the wing's weight.
Prior to the Amazon MARS conference, the omnids were temperamental 'research-only' devices for lab use. Given a three month timeline, the robots had to be modified and made robust for demos with unfamiliar operators, and stay operational for long periods of time.
CAD designed and manufactured the second layer for each omnid with EMI shielding electrical boxes and quick slide out trays. Laser cut the base layers, and sheet metal formed the shielding boxes, resulting in dramatically improved PCB connection fidelity and uptime.
Other tasks included SMD soldering, wire crimping, and robot debugging.
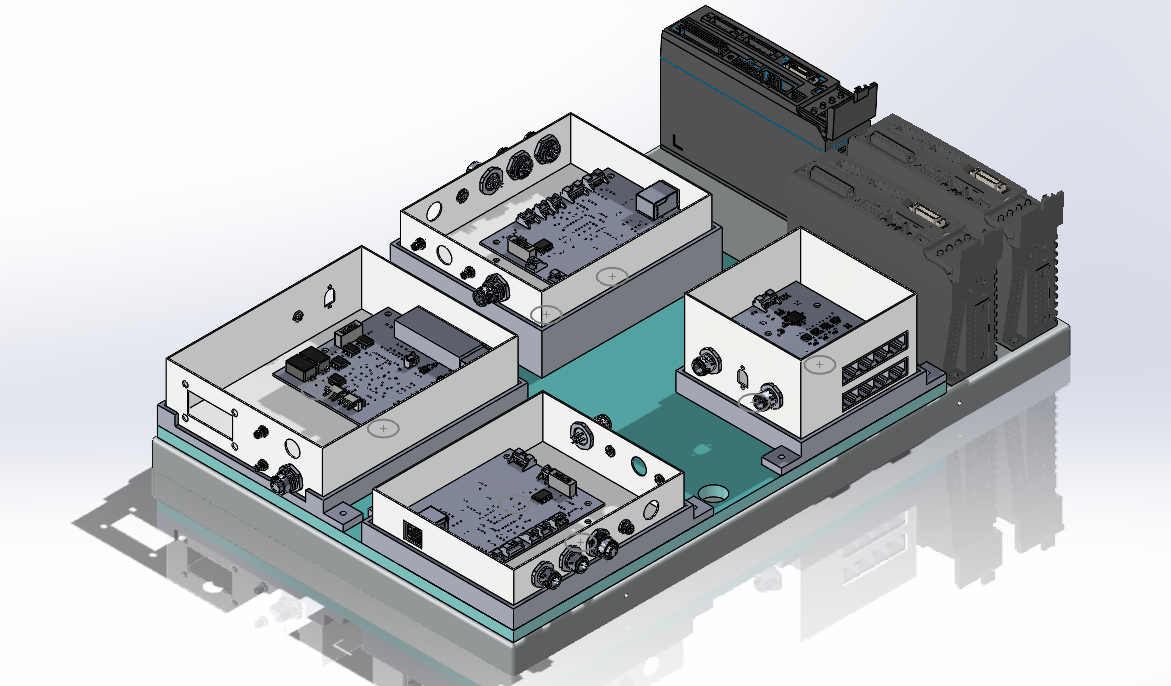
Laser Cut Acrylic Base
1st Version Eboxes and Trays
Final Version Eboxes and Trays
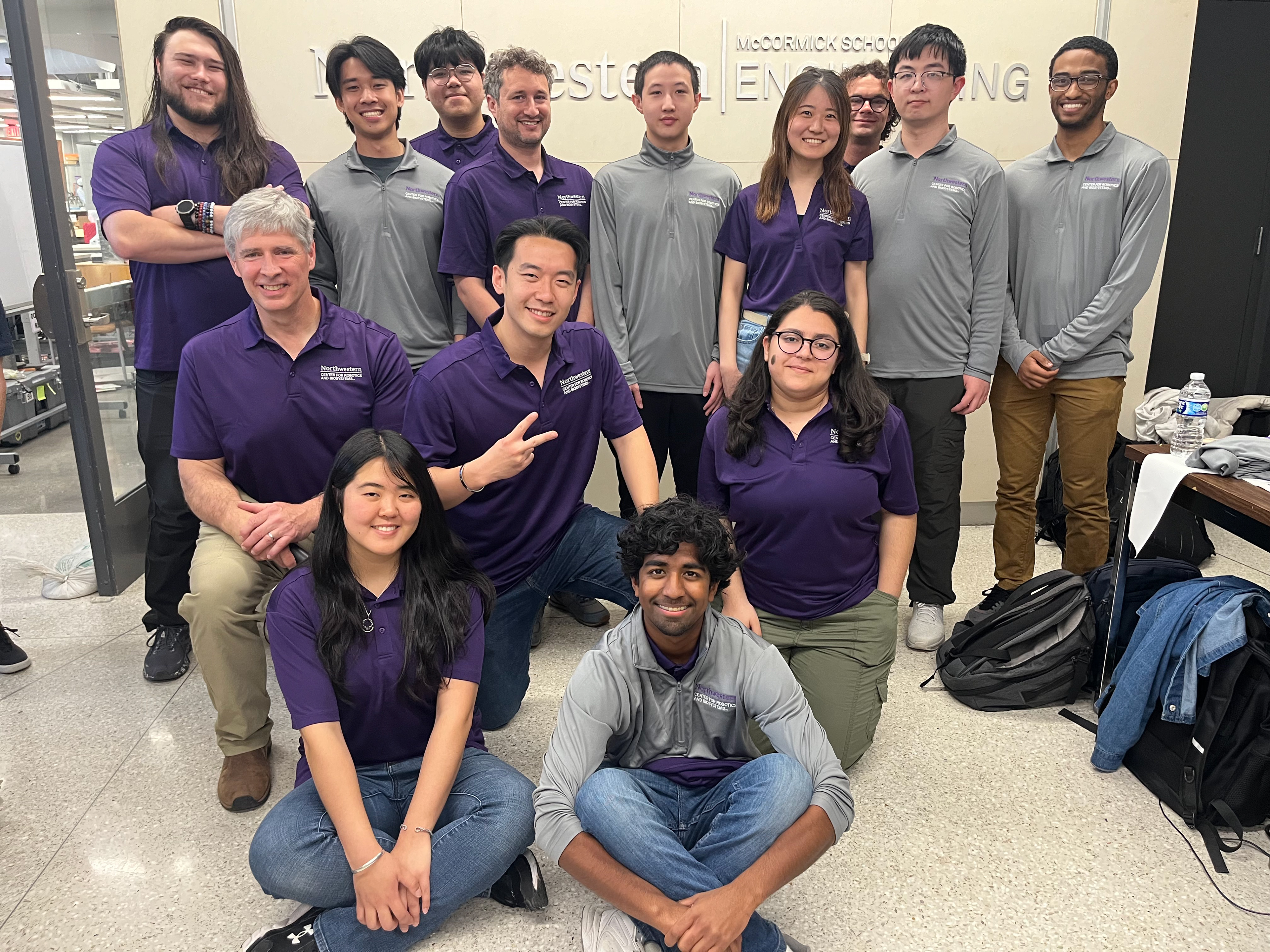
By the time of the conference, the second layer subsystem was fully assembled and integrated to shield the PCBs from EMI, and dust and particles. The slide out trays provided modularity in the event boards had to be swapped out at the conference.
"The students put in a lot of long nights and made a heroic effort to produce this complex engineered system as finals week approached, and the end result was a robust system that worked really well at the conference,” Prof. Kevin Lynch said. “Guests were able to use the robots effectively with zero training."
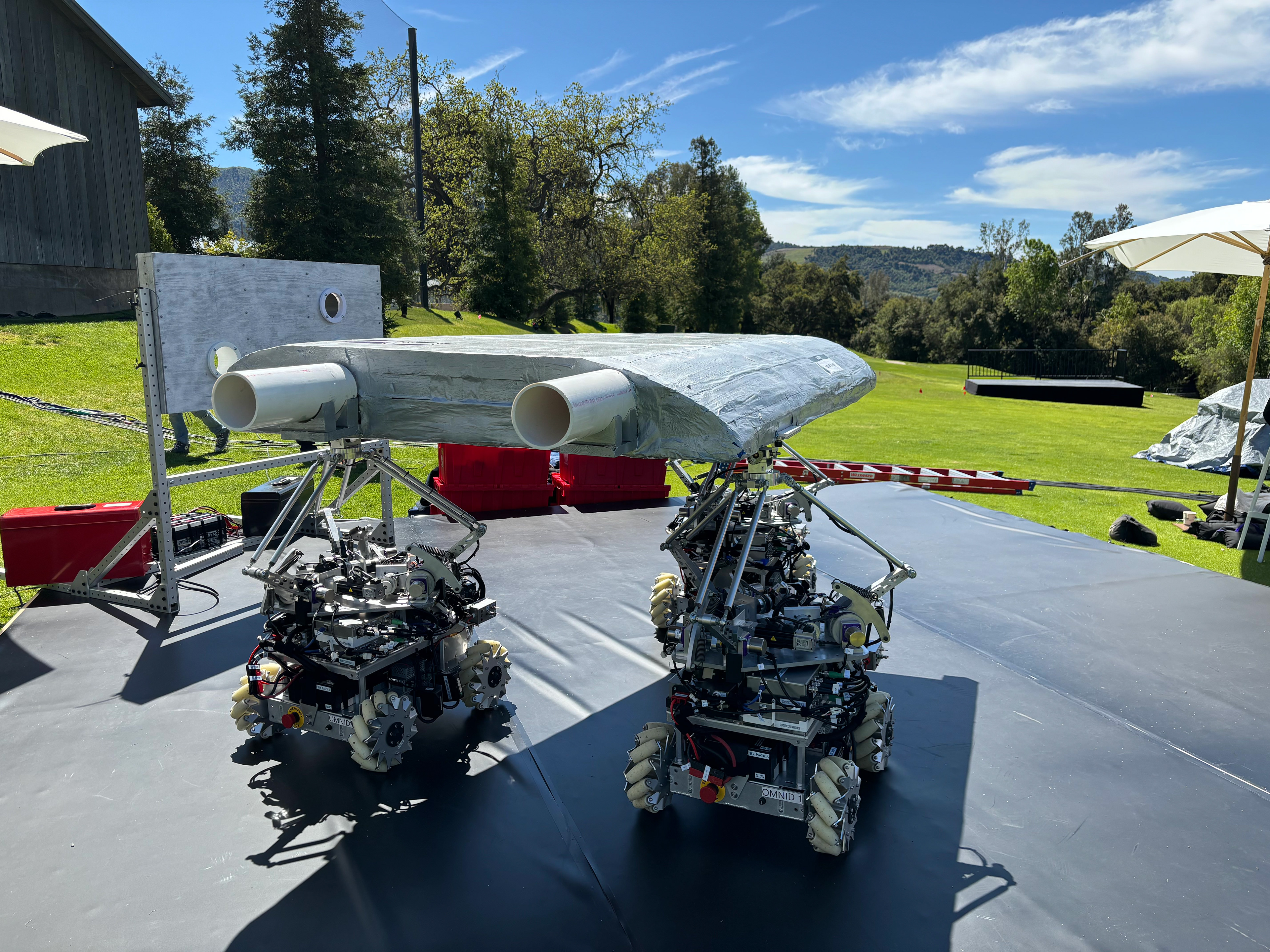